Porosity in Welding: Identifying Common Issues and Implementing Finest Practices for Prevention
Porosity in welding is a prevalent concern that commonly goes unnoticed up until it causes substantial issues with the honesty of welds. In this discussion, we will certainly explore the crucial factors contributing to porosity development, examine its destructive effects on weld efficiency, and talk about the ideal practices that can be embraced to decrease porosity occurrence in welding processes.
Usual Sources Of Porosity

Using dirty or damp filler materials can present pollutants into the weld, adding to porosity problems. To reduce these usual reasons of porosity, extensive cleaning of base steels, proper securing gas choice, and adherence to optimal welding specifications are vital methods in achieving high-grade, porosity-free welds.
Effect of Porosity on Weld Quality

The visibility of porosity in welding can substantially compromise the architectural integrity and mechanical homes of bonded joints. Porosity creates gaps within the weld metal, damaging its overall toughness and load-bearing capacity. These spaces act as anxiety focus points, making the weld a lot more susceptible to splitting and failing under applied tons. In addition, porosity can decrease the weld's resistance to rust and various other environmental aspects, better decreasing its durability and efficiency.
Among the key consequences of porosity is a decrease in the weld's ductility and durability. Welds with high porosity degrees tend to exhibit lower effect stamina and minimized capacity to flaw plastically before fracturing. This can be particularly concerning in applications where the welded components go through dynamic or cyclic loading problems. Porosity can hinder the weld's ability to efficiently transmit forces, leading to early weld failing and possible safety and security hazards in essential frameworks. What is Porosity.
Ideal Practices for Porosity Avoidance
To improve the architectural integrity and high quality of bonded joints, what details actions can be implemented to minimize the event of porosity throughout the welding process? Making use of the appropriate welding technique for the particular product being bonded, such as adjusting the welding angle and weapon setting, can further avoid porosity. Routine examination of welds and instant removal of any issues recognized during the welding procedure are important practices to prevent porosity and generate premium welds.
Importance of Appropriate Welding Techniques
Applying appropriate welding techniques is critical in ensuring the structural integrity and high quality of bonded joints, building on the foundation of effective porosity avoidance procedures. Welding techniques directly influence the total strength and longevity of the welded structure. One key element of appropriate welding methods is keeping the appropriate warmth input. Extreme heat can YOURURL.com result in enhanced porosity due to the entrapment of gases in the weld swimming pool. On the other hand, insufficient warm may result in incomplete fusion, developing potential weak factors in the joint. In addition, using the appropriate welding criteria, such as voltage, existing, and travel rate, is important for attaining sound welds with marginal porosity.
Furthermore, click this the choice of welding process, whether it be MIG, TIG, or stick welding, must align with the details needs of the project to ensure optimal results. Proper cleansing and prep work of the base steel, as well as picking the best filler product, are likewise essential components of efficient welding techniques. By adhering to these best methods, welders can decrease the risk of porosity development and create top notch, structurally sound welds.
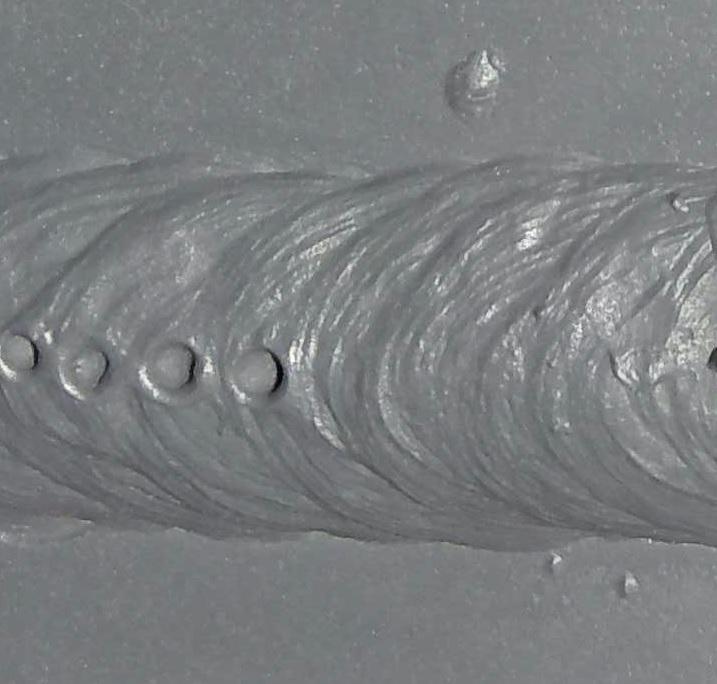
Evaluating and Quality Assurance Steps
Quality control steps play an essential duty in confirming the honesty and integrity of bonded joints. Evaluating procedures are necessary to detect and avoid porosity in welding, making certain the stamina and longevity of the final item. Non-destructive testing approaches such as ultrasonic testing, radiographic testing, and visual evaluation are frequently utilized to determine potential defects like porosity. These methods enable for the evaluation of weld quality without endangering the stability of the joint. What is Porosity.
Post-weld examinations, on the various other hand, examine the last weld for any defects, consisting of porosity, and validate that it satisfies specified criteria. Implementing a comprehensive quality control strategy that includes comprehensive testing treatments and assessments is critical to minimizing porosity issues and ensuring the total top quality of bonded joints.
Final Thought
In conclusion, porosity in welding can be a common issue that influences the top quality official statement of welds. By determining the common sources of porosity and applying best techniques for prevention, such as proper welding techniques and screening measures, welders can ensure premium quality and reliable welds. It is necessary to focus on avoidance techniques to minimize the incident of porosity and keep the stability of welded frameworks.